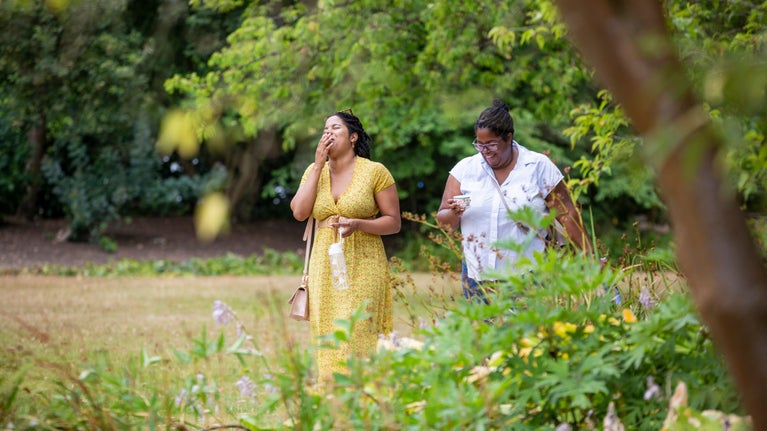
Become a member
Join today and help protect nature, beauty and history – for everyone, for ever. Enjoy access to more than 500 places with National Trust membership.
Concealed under the long sloping roof of this medieval building is a fully restored, working corn mill.
Congleton Road, Nether Alderley, Macclesfield, Cheshire, SK10 4TW
Find out more about our special offers for group visits to Nether Alderley Mill, Cheshire and everything else you need to know about booking and arriving on the day.
Join today and help protect nature, beauty and history – for everyone, for ever. Enjoy access to more than 500 places with National Trust membership.