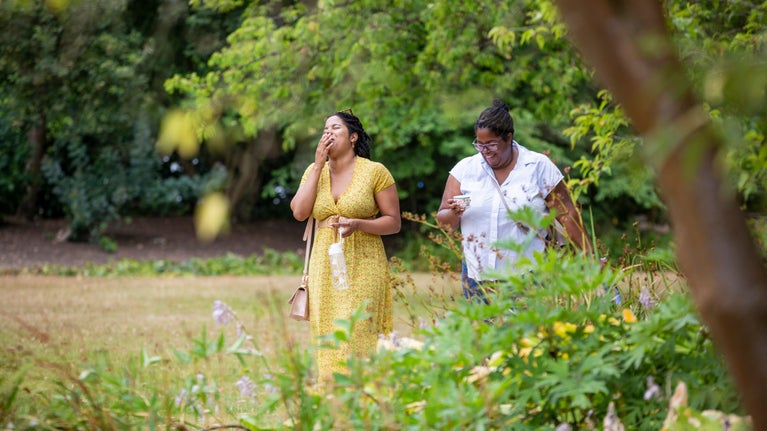
Become a member
Join today and help protect nature, beauty and history – for everyone, for ever. Enjoy access to more than 500 places with National Trust membership.
Picturesque watermill with working waterwheel.
Bourne Road, Colchester, Essex, CO2 8RT
Search our upcoming events, from seasonal trails to community open days.
Plan your school visit to explore the wildlife, history and culture of this historic site with our lesson ideas and resources.
There is limited Blue Badge parking on site. On-road parking is available in close proximity. On site there are grassy paths and slopes, with some steps around the grounds. There is an accessible compost toilet in the grounds, there is also a toilet on the first floor of the Mill. There are picnic tables outside the Mill.
Dogs on leads are welcome at Bourne Mill. This article explains where your dogs can and can't go, the facilities we provide for them and our Canine Code.
Join today and help protect nature, beauty and history – for everyone, for ever. Enjoy access to more than 500 places with National Trust membership.