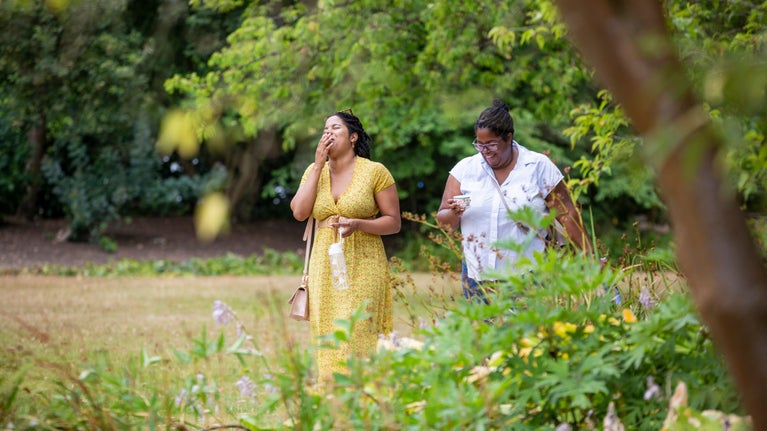
Become a member
Join today and help protect nature, beauty and history – for everyone, for ever. Enjoy access to more than 500 places with National Trust membership.
Iconic Tudor Manor House with wonky angles and quirky character
Newcastle Road, Congleton, Cheshire, CW12 4SD
Asset | Opening time |
---|---|
Little Moreton Hall | Closed |
Last entry to the hall is 4pm. Welcome Building closes at 4:30pm.
Ticket type | With Gift Aid | Without Gift Aid |
---|---|---|
Adult (18+) | £16.50 | £15.00 |
Child (5-17) under 5s free | £8.30 | £7.50 |
Family (2 Adults and up to 3 children) | £41.30 | £37.50 |
e.g. 1 adult, 2 children | £24.80 | £22.50 |
Assistance dogs only in the hall, tea-rooms and garden.
Pre-loved bookshop
Spotter activities available throughout the year.
Mrs Dale's Tea-room and Little Tea-room open from 10.30am serving seasonal hot and cold food, drinks, ice creams, savoury and sweet treats.
Blue Badge parking. Accessible toilet. Steep spiral staircases, uneven floors and cobbled courtyard. Powered Mobility Vehicles and motorised wheelchairs with a maximum width of 0.5 metres can enter Little Moreton Hall. Those that are wider than 0.5 metres can enter the Great Hall where a book of photographs of the upper floors is available, but due to the historic narrow doorways cannot proceed any further. Any Powered Mobility Vehicles wider than 0.5 metres can be left in the courtyard, please speak to a member of our team who can assist with this. Manual wheelchairs are available to borrow.
Powered Mobility Vehicles and motorised wheelchairs with a maximum width of 0.5 metres can enter Little Moreton Hall. Those that are wider than 0.5 metres can enter the Great Hall where a book of photographs of the upper floors is available, but due to the historic narrow doorways cannot proceed any further.
Powered mobility vehicles are not able to enter into Mrs Dale's tea-room but the Little tea-room is accessible.
Level access to Welcome Building where you can find our pre-loved books section.
Powered Mobility Vehicles and motorised wheelchairs with a maximum width of 0.5 metres can enter Little Moreton Hall. Those that are wider than 0.5 metres can enter the Great Hall where a book of photographs of the upper floors is available, but due to the historic narrow doorways cannot proceed any further.
Visual Guide of the upper floors is available in the Great Hall.
Cobbles in the courtyard and spiral stairs within the building.
Available to borrow from the welcome building.
on east side of A34. From M6 exit 17 follow signs for Congleton and join A34 southbound (signed Newcastle) from Congleton
Parking: 100 yards
leave the Macclesfield canal at bridge 86. Map to Hall displayed on towpath
Kidsgrove 3 miles; Congleton 4½ miles
services from Alsager to Congleton (passing close to Kidsgrove), infrequent (not Sundays)
19 July–31 August | Travel through time, without the need for a time machine, from Tudor to present day, as you delve into the history of games in the outdoors. Will you come across a familiar favourite or discover a new game to give a go?
Discover the the iconic Tudor manor house at Little Morton Hall with your group, visit the tea-room, chat to the room guides and living history team, and have a stroll in the garden.
Little Moreton Hall welcomes assistance dogs only throughout the hall, garden and tea-rooms. Access to other dogs is very limited. All other dogs are very welcome on leads on the front lawn, car park areas and the open area outside the moat.
Please use this map to help you plan your visit to Little Moreton Hall.
Iconic wood frame moated Tudor manor house, with wonky angles and quirky character.
Knot garden and borders and traditional viewing mounds. Across the moat is a small orchard with young trees.
Mrs Dale's tea-room offers hot and cold food and drinks. Little tea-room offers takeaway options to eat in the garden.
Pre-loved bookshop selling a range of second-hand books.
While modern life rushes by outside, Little Moreton Hall, encircled by a moat, survives as a Tudor fantasy, transporting you back to another time.
Whether you’re enjoying one of our self-led trails or the wibbly-wobbly floors, there's plenty of free activities to keep the whole family entertained at Little Moreton Hall.
Discover Cheshire’s heritage and nature through grand houses, deer parks, seasonal gardens, woodland, moorland, and even a cotton mill.
The cosy tea-rooms at Little Moreton Hall offer delicious meals and treats all year round and are open Wednesday – Sunday from 10.30am. During the school holidays the tea-rooms are open seven days a week, giving you more chances to pop in and have a brew.
Where are those wandering wolves? Join us at Little Moreton Hall on this free spotter activity, and help us locate the missing wolves. How many will you discover when you visit?
Summer of Play comes to Little Moreton Hall, and we hope you can join us and discover our self-led, blast from the past, time travelling trail!
Discover your inner Robin Hood and have a go at archery at Little Moreton Hall this summer.
We're opening our doors for free entry at Little Moreton Hall as part of Heritage Open Day.
Visit Little Moreton Hall this half term and 'Escape into autumn.' Discover autumn colours and what wildlife gets up to over the season with our free spotter trail.
On your festive wander to look around our 'Deck the Hall' Christmas event, see how many roaming robins you can spot inside and outside of the hall.
Join us this Christmas at Little Moreton Hall for the last year of 'Deck the Hall', and take a step back into the past and celebrate traditions old and new.
A topsy-turvy Tudor house
It’s not your eyes playing tricks on you. Seeing the tumbling architecture of Little Moreton Hall for the first time, engineers in 1990 could not believe their eyes either. This timber-framed building, curled around with a scenic moat, has defied logic for over 500 years. Step back in time inside this higgledy-piggledy house and discover what every day Tudor life tells us about the way we live today.
Find out more
Have a chat with our costumed Living History team on the ground floor, to find out more about how people lived at the Hall. Upstairs, the knowledgeable room guides can answer any questions that you have and remember to ask them about the protective marks carved or burnt into the wooden structure of the building to ward off evil.
Knot just a garden
You’ll find herbs and vegetables that the Tudors would have used for their cooking and medicines surrounding the Elizabethan style knot garden. Take a stroll around the moat to spot creatures great and small who call Little Moreton Hall their home.
Tea-rooms
Enjoy a sandwich and a delicious slice of cake inside the quaint Little Tea Room or soak up the sunshine on the lawn with afternoon tea. You’ll find a different experience in Mrs Dale’s Tea Room with service right to your table, warming dishes and a log-burning stove when it’s nippy.
Discover the ritual protection marks scattered about the house, how the Tudors used to sleep twice a night, and why Little Moreton Hall may be the wonkiest house you’ll ever see.
Work is underway to restore the 500 year old chimneys, to ensure that they are safe, structurally secure and can continue to withstand the impact of the ever-changing weather.
Take a glimpse into the Moreton family letters held at the British Library, transcribed by our research volunteers, and offering a valuable insight into 17th century life.
Explore the objects and works of art we care for at Little Moreton Hall on the National Trust Collections website.
Search for live volunteering opportunities, or register your interest with Little Moreton Hall.
Find out about the supporter groups you can join in Cheshire and Greater Manchester including East Cheshire National Trust Association, South Cheshire Association and The National Trust Chester Centre
Join today and help protect nature, beauty and history – for everyone, for ever. Enjoy access to more than 500 places with National Trust membership.
By sharing your email address you’re agreeing to receive marketing emails from the National Trust and confirm you’re 18 years old or over. Please see our for more information on how we look after your personal data.