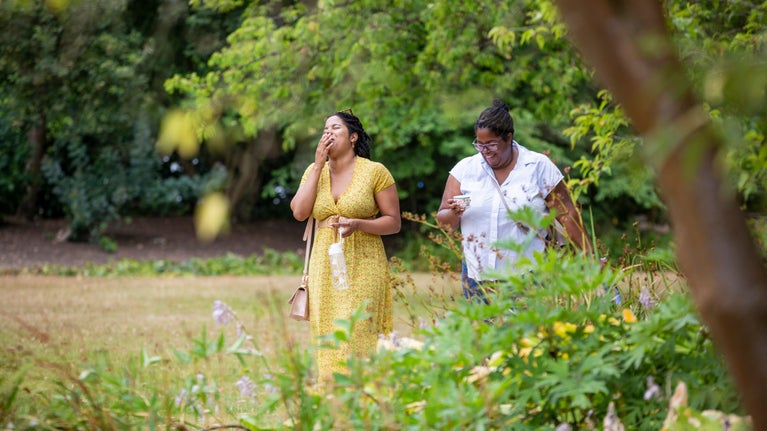
Become a member
Join today and help protect nature, beauty and history – for everyone, for ever. Enjoy access to more than 500 places with National Trust membership.
One of the most spectacular timber framed buildings of medieval England at the heart of village life
Market Place, Lavenham, Sudbury, Suffolk, CO10 9QZ
Asset | Opening time |
---|---|
Guildhall | 10:00 - 16:00 |
Tea-room | 10:00 - 16:00 |
Last admission to the Guildhall 3:30pm and last orders in Tea-room 3:45pm
Ticket type | With Gift Aid | Without Gift Aid |
---|---|---|
Adult (18+) | £11.00 | £10.00 |
Child (5-17) under 5s free | £5.50 | £5.00 |
Family (2 Adults and up to 3 children) | £27.50 | £25.00 |
Family One Adult (1 adult & up to 3 Children) | £16.50 | £15.00 |
Group (Adult 18+) | £9.50 | |
Group (Child 5-17) | £4.75 |
Closest charging points Gas works car park on Water Street CO10 9RN Church Street Car Park CO10 9SA
Drop-off point available. Accessible toilet. Ground floor of Guildhall and parts of garden accessible.
Visitors can be dropped off outside the Guildhall entrance
Take the A1141 off the A1134 which will take you directly into Lavenham High street, then take the turning for Water Street followed by Lady Street which leads you into the Market square, and the Guildhall is straight in front of you.
Parking: Free parking in the village, there is some on street parking as well as some car parks around the village if the Market Place outside the Guildhall is full.
Sat Nav: Postcode CO10 9QZ
4 mile 'Railway Walk' links Lavenham with Long Melford
Sudbury 7 miles
Chambers 753 Bury St Edmunds to Colchester (passes close Bury St Edmunds train station and Sudbury train station)
South Suffolk Cycle Route A1
See what's on at Lavenham Guildhall, from our regular spinning demonstrations and walks to our seasonal trails.
Educational and fun, there's lots for every member of the family to enjoy on a day out at Lavenham Guildhall.
Dogs are welcome at Lavenham Guildhall, but we ask that you follow our guidance in order to keep everyone happy and safe. To find out more, read on.
Groups are welcome at Lavenham Guildhall, when booked in advance. To do so, please call or email the property.
16th-century timber framed Guildhall, exploring the stories of those who have used the building over the last 500 years.
Cosy tea-room with indoor and outdoor seating serving hot and cold drinks, cakes, ice creams, lunches and cream teas.
Courtyard garden with outdoor seating, bug hotel and borders planted with traditional dye plants.
Bookshop stocked full of pre-loved books, CDs and DVDs.
Essex Cultural Diversity Project and the National Trust invite proposals from creative practitioners for a new commission responding to Lavenham Guildhall, a National Trust site in Suffolk. The Guildhall is of great historical significance, emphasised by its location within this renowned historical wool town, and today is enjoyed by around 25,000 visitors per year, as well as featuring as the backdrop to numerous films. We are looking for a project that can connect the past, present and future of the Guildhall; one which recognises the significance of the building’s unique history; explores its current relevance to the local context and can engage both existing and potential communities; and a project that can help articulate shared visions for the future. Budget: £10,000 Deadline: Tuesday 10 June 2025 Follow link for further information.
Every Thursday our spinning volunteers demonstrate the traditional art of spinning wool into the yarn that we see and recognise today. You’ll usually find them in the Main Hall, where you can ask questions to learn more about the history and process of creating traditional cloth and its vital role in Lavenham's past.
Discover the medieval history of Lavenham on an engaging guided walk of the village with one of our knowledgeable volunteer guides. Every Friday from 16 May, at 14:00. Booking essential - please note availability is limited to approx 10 places per walk.
Come and explore a fascinating chapter in Lavenham’s history in our new community room exhibition, 'Lavenham in the 16th Century'. During the height of the wool trade, Lavenham was thriving. It became one of the 14th wealthiest places in England, contributing more in taxes than the cities of Lincoln and York. But things didn’t stay that way. This exhibition tells the story of how Lavenham’s fortunes changed dramatically, leaving behind an incredible legacy of more than 300 listed buildings - and a village full of stories, as we celebrate the 500-year anniversary since the completion of St Peter and St Paul’s Church this year.
From the medieval Guildhall of Corpus Christi to the winding, hidden lanes and historic architecture, there's plenty to discover on a visit to Lavenham village.
Educational and fun, there's lots for every member of the family to enjoy on a day out at Lavenham Guildhall.
Walk amid wild flowers, birds and animals along the disused Great Eastern railway line between two medieval ‘wool’ villages, starting at the Guildhall and finishing at Melford Hall, Long Melford.
Spot rare butterflies and countryside views worthy of Constable, as you explore the woodland community project and an old railway line trail around Lavenham.
Take a break and enjoy coffee and cake when you visit Lavenham Guildhall. Sit outside in the sunny Courtyard Garden or relax inside the Tudor tea-room.
Cosy up in this folky rotunda deep in the woodlands of the Ickworth Estate.
Stay in this characterful Georgian cottage, once the home of the Ickworth estate gatekeeper.
An idyllic stay on the Ickworth estate with a lakeside garden and homely interior.
Discover the medieval history of Lavenham on an engaging guided walk of the village with one of our knowledgeable volunteer guides.
Step into the past and let imaginations run wild with Summer of Play at Lavenham Guildhall.
Set in the lovely village of Lavenham, the Guildhall of Corpus Christi tells the story of one of the best-preserved and wealthiest towns in Tudor England.
When you step inside this fine timber-framed building, you'll feel the centuries melt away. You can discover the stories of the people who have used the Guildhall through its almost-500 years at the heart of its community, and learn about the men and women who have shaped the fortunes of this unique village.
After, you can explore the picturesque streets of Lavenham, lined with shops, galleries and more than 320 buildings of historic interest.
Immerse yourself in 500 years of colourful history at Lavenham Guildhall. Discover the people that shaped the unique building and the nature of Lavenham itself.
Uncover the history of Lavenham village, once a thriving centre of the prosperous ‘blew’ cloth trade and home to the little-known author of a world-famous nursery rhyme.
Explore the objects and works of art we care for at Lavenham Guildhall on the National Trust Collections website.
Learn about the process of limewashing at Lavenham Guildhall, Suffolk, why it’s so important for timber-framed buildings and how we carry out the project every five years.
Volunteers play a vital role in helping us to look after Lavenham Guildhall. Find out what's involved in being a volunteer, and how you can apply to join the team.
Join today and help protect nature, beauty and history – for everyone, for ever. Enjoy access to more than 500 places with National Trust membership.
By sharing your email address you’re agreeing to receive marketing emails from the National Trust and confirm you’re 18 years old or over. Please see our for more information on how we look after your personal data.