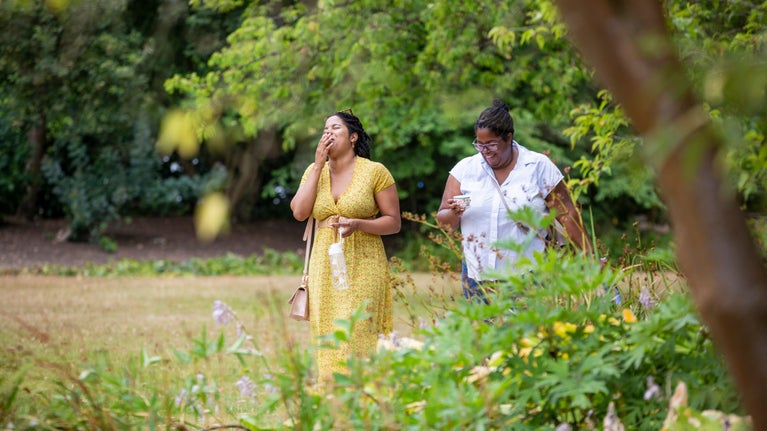
Become a member
Join today and help protect nature, beauty and history – for everyone, for ever. Enjoy access to more than 500 places with National Trust membership.
Free to enter Ancient watermill, café with island garden and wildlife spot in the heart of Winchester
Bridge Street, Winchester, Hampshire, SO23 9BH
Asset | Opening time |
---|---|
Watermill | 10:00 - 17:00 |
Cafe | 10:00 - 17:00 |
Second-hand bookshop | 10:00 - 17:00 |
Please note our Watermill is currently not operating and the area may have random closures throughout the year whilst it is being repaired.
Please contact the property via email to discuss availability and pricing.
No on-site parking. Entrance to the mill is via a low-gradient ramp up from the front courtyard. Stairs with handrail to the entrance of the Mill space, down to the millrace and out to the Island Garden.
Take junction 9 from north M3, junction 10 from south M3.
Parking: We have no parking on site. The nearest parking is at Chesil car park (Not NT) or use the park and ride from St Catherine's to Winchester. (Not NT) See Winchester City Council's parking webpage for more information - http://www.winchester.gov.uk/parking
Sat Nav: Do not use postcode as we have no parking on site.
South Downs Way, King's Way, Itchen Way -- all pass through or finish at Winchester.
Winchester railway station is 1 mile away.
Regular local buses from the surrounding areas stop nearby.
Take a look at the map of Winchester City Mill to help plan your visit.
Discover delicious treats and refreshing beverages at our riverside café, whether sampling an iced latte or our scone of the month there is something for everyone.
A rare surviving example of an urban corn mill in Winchester, dating back at least 1000 years to the reign of King Alfred.
Our café has the perfect field to fork story, and housed in the most beautiful setting of the Mill. Seating is available outside in our Island Garden overlooking the tranquil River Itchen.
Delve into the goodies on our bookshop shelves, all donations go towards looking after this very special place.
A small but perfectly formed oasis in the middle of the city with views either side over the River Itchen.
Situated in the heart of the mill, the café at Winchester City Mill is an ideal spot for tucking into delicious baked goodies and a hot or cold drink while soaking up the atmosphere of the 1,000-year-old watermill. Our baked goods are freshly made here each day by our talented team, coffee is Fairtrade and 100% Arabica with notes of butterscotch and shortbread, with a changing selection of fresh lunch options available.
Grab a bite to eat in our café, spot otters in the river using the otter-cam or learn about how the Mill has been such an important part of Winchester's history.
Whether the sun is shining or the rain is pouring, discover why Winchester City Mill is ideal for a family day out.
Join us for a unique talk and demonstration lead by one of our expert millers.
A guided ‘walk and talk’ tour presenting the most interesting features of Winchester City Mill.
Join us for family quern demonstrations and learn all about milling and how we make flour!
Out There Actions theatre tell the true story of a curious adventure experienced by two cows at Winchester City Mill in September 1849. A ten-minute show for the whole family, performed on demand, throughout the day.
Winchester City Mill has stood at the heart of the historic city of Winchester, the capital of King Alfred’s Wessex, since at least Saxon times. With a history of over 1000 years, Winchester City Mill is one of the oldest watermills in the UK.
A rare surviving example of an urban corn mill, the City Mill was rebuilt in 1744. Having entered the care of the National Trust in the late 1920’s, the City Mill was partially restored in 2004. In early 2023, the waterwheel was decommissioned and so the next phase is to raise money for a new wheel so we can begin milling once again!
Inside, you’ll discover more about the mill’s long and fascinating history. Learn how we intend to return to milling traditional stoneground wholemeal flour using the power of the River Itchen and have a short guided tour by one of our wonderful guides (subject to availability).
The City Mill is home to a wide variety of wildlife including kingfishers, grey wagtails, wild trout and water voles, which can be spotted from our tranquil island garden. Watch our city otters’ adventures from regularly updated archive footage and view the live feed from our cameras along the river.
The City Mill is also the official gateway to the South Downs National Park, providing a wide selection of information for those wishing to explore local walks and the attractions found within the South Downs, including the many historic National Trust properties.
Discover the history of Winchester City Mill, probably the oldest working watermill in the country, from its Saxon origins to modern-day rebirth with the National Trust.
Our mill wheel has come to the end of its life and has had to be decommissioned. We are now looking to the future and to restore the wheel and revive our flour production once again.
Find out more about the step-by-step process and how a water-powered mill works, a tradition which has been passed down for centuries.
Search for live volunteering opportunities, or register your interest with Winchester City Mill.
Join today and help protect nature, beauty and history – for everyone, for ever. Enjoy access to more than 500 places with National Trust membership.
By sharing your email address you’re agreeing to receive marketing emails from the National Trust and confirm you’re 18 years old or over. Please see our for more information on how we look after your personal data.