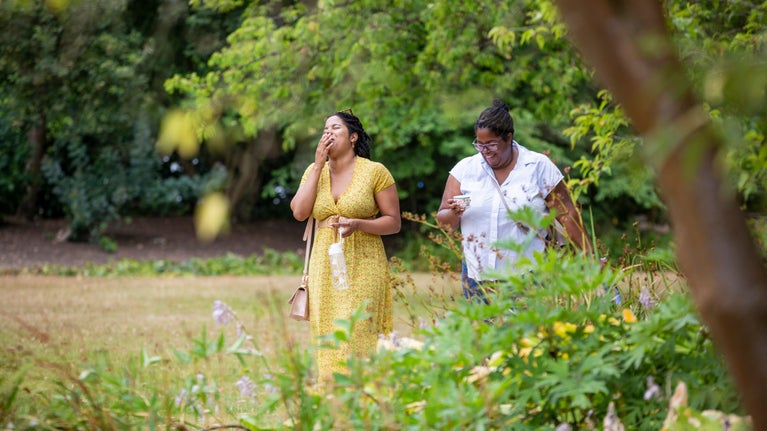
Become a member
Join today and help protect nature, beauty and history – for everyone, for ever. Enjoy access to more than 500 places with National Trust membership.
Impressive Cornish beam engines and industrial heritage at the heart of the Cornish Mining World Heritage Site. Open by pre-booked tours.
Pool, near Redruth, Cornwall, TR15 3NP
Book a visitSee our upcoming events, exhibitions and tour offers here.
East Pool Mine is open for guided tours and it is recommended that you book your visit in advance. If you're planning a visit to East Pool Mine, read this article to find out everything you need to know.
We believe that East Pool Mine should be accessible for all. There are many ways that we try to make your visit as accessible as possible, find all the information you need to discover how you can best access this special place.
East Pool Mine invites you to visit our diverse education offers, designed to be adaptable to suit your needs and support the curriculum. Our dedicated team can help you plan your visit to ensure that you get the most out of what we have to offer.
Not a member? If you're planning a trip to Cornwall, buy a National Trust Explorer Pass to enjoy entry to most of the places in our care. With 4-, 8- and 14-day options available, the pass can be tailored to fit your trip. Discover where you can visit with the Explorer Pass and how to buy yours.
Join today and help protect nature, beauty and history – for everyone, for ever. Enjoy access to more than 500 places with National Trust membership.