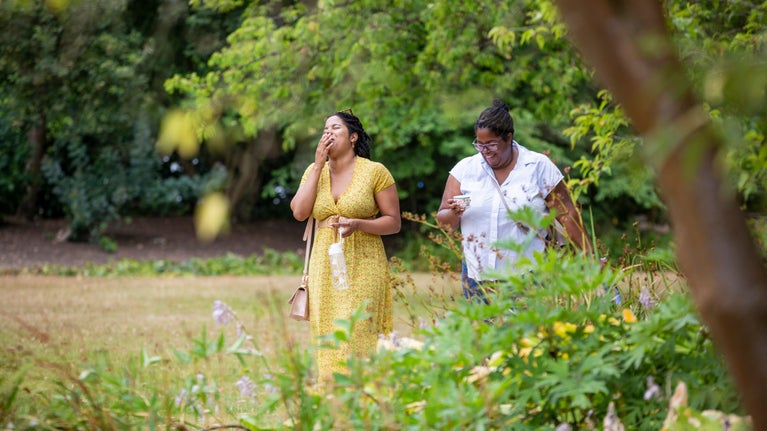
Become a member
Join today and help protect nature, beauty and history – for everyone, for ever. Enjoy access to more than 500 places with National Trust membership.
The working mill is the beating heart of Quarry Bank. Set in picturesque gardens and countryside, explore one of Britain's greatest industrial heritage sites.
Styal, Wilmslow, Cheshire, SK9 4HP
Asset | Opening time |
---|---|
Mill | 10:30 - 17:00 |
Apprentice House | 11:00 - 16:00 |
Quarry Bank House | 11:00 - 16:30 |
Garden | 10:30 - 17:00 |
Upper Garden Cafe | 10:30 - 16:45 |
Weaving Shed Restaurant | 10:30 - 17:00 |
Mill Shop | 10:30 - 17:00 |
Second-hand bookshop | 10:30 - 17:00 |
Visitor reception | 10:30 - 17:00 |
Estate | 08:00 - 20:00 |
Car Park | 08:00 - 20:00 |
The Ice Cream Parlour in the Mill Yard is open at weekends and during school holidays only. Visits to the Village Hub and Workers Cottage are available, please ask the team at Visitor Reception for further details.
Ticket type | With Gift Aid | Without Gift Aid |
---|---|---|
Adult (18+) | £23.10 | £21.00 |
Child (5-17) under 5s free | £11.60 | £10.50 |
Family (2 Adults and up to 3 children) | £57.80 | £52.50 |
One adults & three children | £34.70 | £31.50 |
Located near the Mill Yard the play area will keep little ones busy as they take on the trim trail and have fun in the playhouse.
The popular second-hand bookshop can be found in the Mill Yard.
The Upper Garden Café can be accessed by members and paying visitors, and dogs are welcome.
Please respect our neighbours and park in the main visitor car park rather than the village.
Located near Visitor Reception
Dogs on leads welcome around the wider estate and on a short lead in the mill yard, garden, Styal village, outdoors at the Garden Café and footpaths through the main visitor areas of Quarry Bank.
Six 11KW electric vehicle charging points are available in the main car park. Chargers can be accessed using mobile app, RFID card, or contactless payment device. Visit our EV charging partner, RAW Charging's website to download the app before your visit. Chargers are only available to visitors during property opening hours.
Electric vehicle charging point - more informationThe whole family can explore, enjoy a visit to Quarry Bank. A busy events calender and family-friendly facilities means you can find something for everyone, and make memories.
Guided tours are available for the Apprentice House and The Workers Cottage. Pre-booking is not possible. When you arrive, please go to Visitor Reception to book on to a tour.
Outdoor picnic areas can be found near the Upper Garden toilets, in the playground and on the Mill Meadow. On weekends and during school holidays the indoor lunch rooms are open.
The weaving Shed Restaurant is in the Mill Yard
The shop can be found in the Mill yard.
Toilet facilities can be found in the mill yard and upper gardens. Facilities include baby change, and a Place to Change Facility.
Blue Badge Parking. Place to Change toilet facility. Mill lift for wheelchair users. Shuttle buggy service. Steep paths.
Accessibility guides can be found at visitor reception and entrance to the gardens.
A Place to Change facility including a changing bench and hoist can be found in the Mill Yard. An accessible toilet can be found in the Upper Garden behind the café.
Braille guide on the mill is available on request at visitor reception.
On right-hand side of the car park are 16 designated parking spaces on a flat, firm surface. These spaces are for use of visitors holding an official Blue Badge. If you need to park close to the entrance but do not have a Blue Badge, you can ask at visitor reception for a one-day pass to use those bays. Visitor reception is 75m from the parking bays.
Induction hearing loop in Visitor Reception, both the Mill Yard and Garden shops, as well as the Upper Garden Café, Weaving Shed Restaurant and Ice Cream Parlour.
Large print guide on the mill are available on request at visitor reception.
Mill café is 40m from the cobbled mill yard down a sloped flagstone path leading to a level entrance.
Garden shop is 250m from visitor reception and 30m from the garden café, across essentially level compacted gravel or stone-flagged surfaces. Level entrance to second-hand book shop. Access to mill shop by stone stairs with seven steps with a handrail on both sides, or by a powered platform lift for wheelchairs and buggies.
We want to make sure that Quarry Bank is equally accessible for all visitors. The historic buildings and landscape that we care for present challenges in creating access for all, but we have taken steps to ensure that as many people as possible are able to experience Quarry Bank’s story. Please visit the Access at Quarry Bank page for more information.
There is a lift in the Mill and in the Weaving Shed for those who require an accessible visit.
Motorised wheelchairs permitted within mill but due to narrow nature of some areas maximum width restriction 900mm. Powered mobility vehicles not permitted within mill. Powered mobility vehicles not allowed in glasshouse due to narrowness of space. Due to narrow spaces in the Apprentice House, power wheelchairs & power mobility vehicles not permitted.
Photobook in Apprentice House
A powered mobility vehicle (Tramper) is available to borrow. You'll need to book this in advance by calling 01625 445864. You'll be asked where you wish to use it so it can be ready for you there when you arrive.
This facility, located in the Mill Yard, includes a hoist and changing bench.
Available in the Mill Yard Shop.
The shuttle buggy service offers transfers between visitor reception, the mill yard, (for access to the mill, the mill shop and toilets) the Apprentice House, the garden, and Styal village. Due to narrow footpaths, the drop-off point is at the Methodist Chapel, 250m from the Village Hub. The buggy can carry a wheelchair if it can be folded.
Virtual tours of the workers cottage and the Apprentice House are available upon request.
Four 69cm-wide wheelchairs to borrow. They're not self-propelled and you must have a helper to push, but they can pass through most doorways on the site, with some exceptions inside the mill.
Styal train station is 1/2 mile walk/ 12 minutes from Quarry Bank. Manchester Airport is 2 miles away; Wilmslow train station is 2 miles away, approximately a 40 minute walk.
As a thank you for arriving car-free, enjoy 10% off in our restaurant, café or ice cream parlour, when you show a bus or train ticket with the day’s date on it, or a bike helmet. Find out more about exploring car-free
The Bollin Valley Way passes close by - with access to Quarry Bank
National Routes 85, 558 and 'Heritage loop' pass nearby.
As a thank you for arriving car-free, enjoy 10% off in our restaurant, café or ice cream parlour, when you show a bus or train ticket with the day’s date on it, or a bike helmet. Find out more about exploring car-free
Quarry Bank is located off the B5166. Follow the A555 and exit at the Hollin Lane/ Styal Road junction. Follow the brown oak leaf heritage signs. Please respect our neighbours and park in the main visitor car park rather than the village.
Parking: Six electric vehicle charging points are available. See ‘Facilities’ for more information. Drivers will require their own cables to charge
Sat Nav: Use SK9 4HP and follow brown heritage signs. WHAT3WORDS ///teeth.fine.dress
Travel the green way and help us preserve this special place. As a thank you for arriving car-free, enjoy 10% off in our restaurant, café or ice cream parlour, when you show a bus or train ticket with the day’s date on it, or a bike helmet. Find out more about exploring car-free
19 July – 1 September | Come rain or shine, there’s fun for all the family at Quarry Bank. Inside the huge mill, there's a brand-new Play Hub where little ones can dress up, put on puppet shows dive into soft play and enjoy giant board games. Outside you can play nature bingo, race through the maze or build your own adventure. Different activities daily.
Plan your family day out to Quarry Bank and discover all the family-friendly things to do no matter the weather. From exploring the mill, to enjoying one of our seasonal trails around the property.
We want to make sure that Quarry Bank is accessible to as many people as possible. Here's what you need to know about accessing the mill, facilities, gardens and historic buildings.
Dogs are welcome at Quarry Bank, and with 400 acres to explore, there’s plenty of space for them to bound, sniff, jump and splash through the estate. Quarry Bank is a two pawprint rated place.
Wander through the dramatic valley garden, stroll by the river and tune into the sights and sounds of the season as you explore this rare retreat where nature and industry collide.
Find out about group visits to Quarry Bank, or how an educational trip to the property can enhance your students’ learning.
Rare surviving eighteenth-century cotton mill, built by the industrialist Samuel Greg, with working heritage machinery.
Home of the apprentices and superintendents. Up to 90 children were housed here, working 10-hour days in the mill.
Elegant Georgian family home, built for the Greg family. Located next to the mill and overlooking the river and gardens.
Picturesque gardens on the banks of the river valley. Restored glasshouses and kitchen garden.
400 acres of beautiful woodland and countryside surrounding the River Bollin.
Early nineteenth-century village, built by the Greg family for the mill workers. Village hub with an exhibition, and workers' cottage.
A small play area for little ones to enjoy, with outdoor seating located nearby.
Weaving Shed Restaurant, dog friendly Upper Garden Café and Ice Cream Parlour. Browse the Mill Shop and the second hand bookshop.
Summer of Play is back – bigger and better than ever, with two exciting hubs of activity for families to enjoy.
Join us in the upper walled garden for an enchanting theatre experience. We have three captivating productions for you to choose from. A Shakespeare double bill, a historical comedy, and a fun-filled family show.
Brought to you by the producers of Christmas at Dunham Massey, Halloween at Quarry Bank returns with a spine-tingling night of thrills, chills, and glowing surprises.
Plan your family day out to Quarry Bank and discover all the family-friendly things to do no matter the weather. From exploring the mill, to enjoying one of our seasonal trails around the property.
Uncover the story of Quarry Bank, once one of the largest cotton manufacturers in the world and home to a complete Industrial Revolution community.
Wander through the dramatic valley garden, stroll by the river and tune into the sights and sounds of the season as you explore this rare retreat where nature and industry collide.
Pull on your walking boots and stride out on a walk through the 400-acre estate. Follow the river through woodland to discover a historic landscape, bursting with wildlife.
Discover Cheshire’s heritage and nature through grand houses, deer parks, seasonal gardens, woodland, moorland, and a wonky Tudor house.
Explore the Southern Woods at Quarry Bank to find the jaw dropping display of bluebells carpeting the bank next to the River Bollin. As the river twists and turns alongside this woodland walk, keep your eyes out for other hidden gems.
Discover the wider estate at Quarry Bank and see the Apprentice House, Styal Village and the Northern Woods on this circular walk, with lush fields and woodland areas with huge redwoods, rare rhododendrons and folly bridges.
Explore the wider estate of Quarry Bank, Cheshire on a 6.9km loop trail which explores Arthur's Wood
Explore the Western Woods at Quarry Bank, Cheshire. Enjoy the sights and sounds of the River Bollin, and take in the stunning views from the Morley Path, looking down over the valley and the tree canopy below.
Looking for some refreshment? Choose from three venues at Quarry Bank, which include a riverside restaurant and a garden café. Each of them offers a range of hot and cold meals, snacks, cakes and bakes.
Discover unique fabrics woven inside the mill and locally made products, as well as National Trust homewares, gifts, garden essentials and more in our shop.
On the Lyme estate and deer park, this Edwardian cottage looks out over lush green countryside.
Tucked away on the glorious Lyme Park estate, Lyme West Lodge is a picture-book pretty Edwardian cottage set in leafy woodland.
This is your chance to see what life was like for the crowded families in the village
Join us for hours of indoor fun – all part of our Summer of Play
We are excited to be part of HistoryScapes, a new app that brings the history of Quarry Bank to life.
Step inside the Mill to join Sir Monty Webber the moth on his quest to find food and make friends!
Enjoy a behind the scenes look at how the hydro turns the power of the River Bollin into electricity
The guided group toddler walks will take families on a short walk; to experience nature and allow little ones to roam and explore at their own pace.
Join our ranger team for a series of seasonal nature walk through the woodlands at Quarry Bank
At Quarry Bank you can discover a complete industrial community and experience the very different worlds of owner and worker, who lived and worked here side by side.
Discover what it was like to work in a cotton mill. Experience heritage machinery in action and feel the floors shake beneath your feet as the spinning machines turn and the looms weave. Find out about the life and legacy of Samuel Greg, the founder of Quarry Bank.
Explore the Greg family home, Quarry Bank House, and wander through the stunning picturesque gardens that rise up the banks of the river valley, offering stunning views and spectacular changes through the seasons. By contrast, take a guided tour of the Apprentice House to step into the lives of the pauper children who worked in the mill. Stroll to Styal village to see how many of the other workers lived. Styal remains a thriving community today and we ask you to be mindful of our tenants' privacy.
On the estate there are acres of woodland to explore. Follow the meandering path of the river Bollin and cross the folly bridges as you look out for an array of wildlife and beautiful views.
Step inside the mill which led the way into the Industrial Revolution and experience the machines in action. Visit the homes of mill owner and worker to see what life here was like.
Find out more about the wartime roles of the men and women of the Greg family: their brave contributions to the war effort and the tragic consequences for the family.
In collaboration with Findmypast, we've been exploring the 1921 Census of England and Wales. It's helped us get closer to the lives at Quarry Bank, where we've been able to trace the community and family relationships between the Styal residents and the cotton mill. Discover more about these stories, as well as research from nine other places in our care. By clicking this link, you'll enter a third-party operator's website, Findmypast. Please see their separate privacy policy on how they handle your data.
We are excited to be part of HistoryScapes, a new app that brings the history of Quarry Bank to life. HistoryScapes aims to help visitors explore historic landscapes and discover more about the history of the places cared for by the National Trust.
Fabric produced on 19th century Lancashire looms at Quarry Bank, is being used to make a new range of clothing by celebrity tailor Patrick Grant.
Keep up with the latest updates from the River Bollin Project as we work to improve the health of the river along the catchment at Quarry Bank.
Discover more about the £9.4 million project to restore Quarry Bank in Cheshire for future generations to enjoy, and discover how the work was funded.
A major flood event over the New Year period alongside a period of heavy snowfall has caused significant damage at Quarry Bank. Find out how you can support the recovery.
We have had to take the difficult decision to permanently close Giant’s Castle footbridge.
From tour guiding to caring for the gardens and woodlands, find out about the volunteer roles available at Quarry Bank and how to apply to join the team. We also care for Nether Alderley Mill, click to find details of opportunities to volunteer at this hidden gem.
Find out about the supporter groups you can join in Cheshire and Greater Manchester including East Cheshire National Trust Association, South Cheshire Association and The Manchester Centre.
Quarry Bank is passionate about reaching out to young people aged 16-25. Join us to make new friends, gain experience, and design great new events.
Holding thousands of objects & papers, discover how Quarry Bank’s nationally significant archive reveals the stories of a complete Industrial Revolution community.
We need your help to care for the historic buildings, gardens and woodlands here at Quarry Bank
Could plant 50 square metres of wildflower meadow ideal for bees and other pollinators
Join today and help protect nature, beauty and history – for everyone, for ever. Enjoy access to more than 500 places with National Trust membership.
By sharing your email address you’re agreeing to receive marketing emails from the National Trust and confirm you’re 18 years old or over. Please see our for more information on how we look after your personal data.